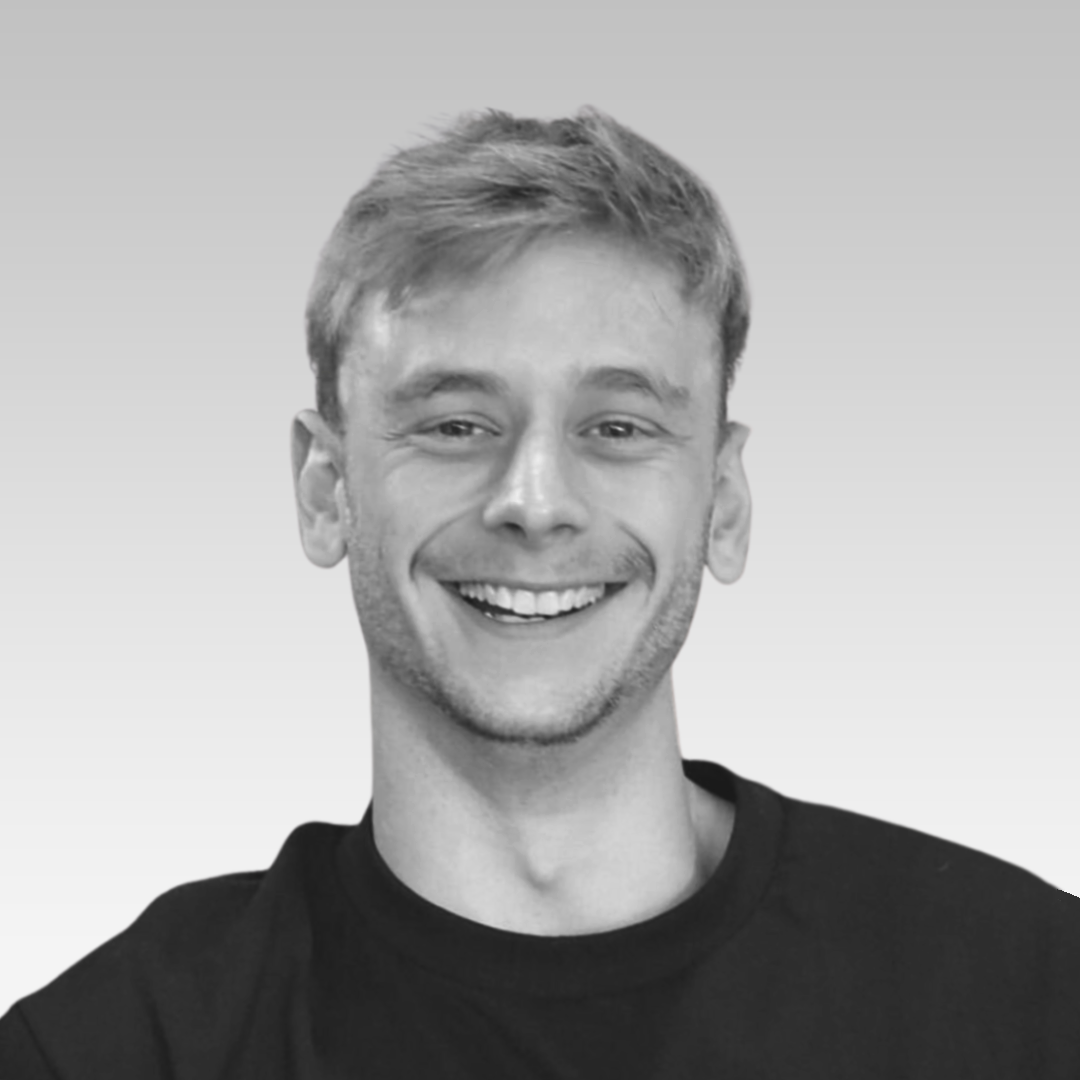
The evolution of manufacturing
Throughout the history of the manufacturing industry, companies have leveraged new technology to optimize their operations. The four industrial revolutions mark stages in the evolution of the industry's use of technology. The first began with steam engines, the second introduced electricity and assembly lines and the third brought computers and automation.
In the current day, the fourth revolution is happening, with the emergence of “Smart Manufacturing” where data and analytics are integrated into business operations.
“The Fourth Industrial Revolution is still in its nascent state. But with the swift pace of change and disruption to business and society, the time to join in is now.” - Gary Coleman, Global Industry and Senior Client Advisor, Deloitte Consulting
What is predictive analytics?
Predictive analytics is a branch of data analytics, which uses historical data to train machine learning models to predict the most likely future outcomes. Predictive analytics can identify previously hidden patterns and allow a company to make data-driven decisions in real time, that are more accurate than theoretical physical models.
Predictive analytics in manufacturing
With increased competition from a globalized market and uncertainty around energy costs, manufacturing companies have already begun turning to predictive analytics to maximize efficiency and reduce costs.
The industry is strongly suited to utilize predictive analytics due to a rapid increase in the volume of high-quality manufacturing data generated, the first, and most crucial aspect for accurate and reliable predictions.
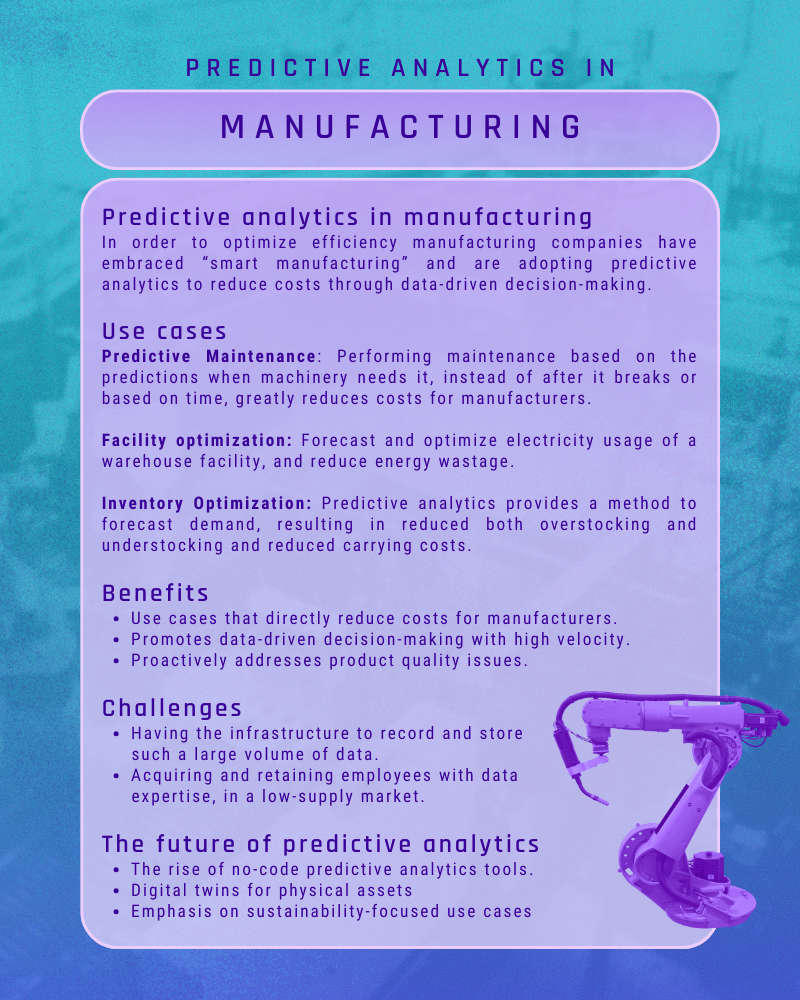
Key components of predictive analytics
To implement predictive analytics effectively and ensure results are accurate and reliable there are several essential components to consider.
Data collection
The first step in predictive analytics is collecting high-quality data, which is abundant in the manufacturing industry. This is, in part, thanks to IoT sensors that connect manufacturing systems to the internet, allowing data to be collected from physical events so that predictions can be generated from machine learning models.
Data preprocessing
Manufacturers have invested heavily in accumulating data, to truly tap into its power the raw data must first be prepared so that it is ready for machine learning algorithms. To get the data machine learning ready, it must be structured properly, and issues such as inconsistent formatting, missing values, outliers, and noise must be resolved. This process is called data pre-processing and it is an integral step in generating reliable and performative predictions.
Model building
Once the data has been collected and prepared, the next step is model building. This process involves training machine learning algorithms on the prepared dataset, where the algorithms discover relationships between variables and trends in order to make predictions on unseen test data. The most appropriate model depends on the data and type of problem being solved. For example, regression and classification algorithms predict different either numerical values or a class respectively, but both require training data to have labeled training data to learn, known as supervised learning. Clustering automatically groups like data points, and doesn’t require labeled data, known as unsupervised learning.
Model evaluation
Model performance evaluation helps quantitatively determine how the model performed against the test data. This step also provides a comparison point to compare one trained model algorithm against another to determine which one is optimal for the problem. Metrics such as precision, recall, and F1-score are used to assess the accuracy and reliability of each model algorithm. These metrics are obtained via the holdout method or k-cross validation method.
Predictive analytics use cases in manufacturing
Now that you’ve got an idea of what predictive analytics is and the process of implementing it, let’s go through some use cases that are already being used.
Predictive Maintenance
In the past, either reactive or preventative maintenance was performed on machinery and equipment. Reactive maintenance involves unplanned shutdowns resulting in lost production, and preventative maintenance often results in unnecessary servicing based on time. Predictive analytics in combination with data from IoT sensors, allow manufacturers to predict when a machine is likely to break and take proactive measures to address the problem. Studies have shown predictive maintenance saving 8-12% over preventative maintenance, and 30-40% over reactive maintenance.
Read further on predictive maintenance.
Facility optimization
Manufacturing operations incur significant costs due to electricity consumption from running machinery, heating, HVAC, and lighting. Predictive analytics provides an opportunity to optimize facilities, reducing energy wastage and costs by forecasting consumption.
Read further on facility optimization.
Demand Forecasting
Inventory management is critical for manufacturers, overstocking can tie up capital, and understocking can lead to missed sales opportunities. Predictive analytics means that manufacturers can forecast demand and have an optimal just-in-time inventory management system, according to the needs of their customers at any time. This leads to improved profitability through reduced carrying costs, which can represent 20-30% of the total inventory value.
Read more about demand forecasting.
Benefits of predictive analytics in manufacturing
The benefits that predictive analytics brings to the table depend on the use case, but there are some general advantages that manufacturing companies usually see regardless of the application.
Cost reductions
Implementing predictive analytics often leads to direct cost savings for manufacturing companies, such as reduced machinery downtime, optimal inventory stocking, or reduced peak demand electricity usage and wastage.
Data-driven decision-making
Predictive analysis empowers data-driven decision-making and effective action. These decisions have improved quality and velocity that consider changing market and production conditions, as well as customer demands.
Improved product quality
Data recording IoT devices like sensors, scales, and cameras can be used in conjunction with predictive analytics to proactively address product quality issues, and fine-tune the production process so that they meet or exceed industry standards.
Challenges in implementing predictive analytics
Despite the potential, there are several challenges that you’ll face when implementing predictive analytics, and understanding the hurdles is vital to avoid pitfalls.
Data Collection
While the manufacturing industry has come a long way in accumulating high-quality data, it’s not always the case for every company. Devices to record data can be expensive, and even with them, ensuring data is collected accurately, consistently, and in real-time can be a hurdle.
Data Storage
Another challenge regarding data is having the appropriate information infrastructure to store and manage such a large amount of incoming data. Having a database or data warehouse that makes the data readily accessible is important to make a predictive analytics project work.
A lack of machine learning expertise
Predictive analytics has historically required a plethora of in-house talent to set up and utilize the findings. Data scientists and data engineers are in high demand and low supply, making acquiring and retaining talent difficult.
The future of predictive analytics in manufacturing
Even in its current state, predictive analytics is drastically raising the standard for manufacturing operations. As the technology improves and adoption grows, the possibilities for future applications are endless.
Self-serve predictive analytics
Self-serve predictive analytics is growing rapidly, and tools providing a way to utilize predictive analytics without coding is the future of the technology. Tools such as the AI & Analytics Engine empower a broader range of professionals to utilize predictive analytics without needing to code, making it more accessible to more companies in the manufacturing industry without access to in-house data expertise.
Digital Twins
Digital twins refer to virtual replicas of physical assets, which are used to simulate the operating behavior. Using digital twins provides a way for manufacturers to capture a greater volume of data compared to a real-world machine, and experiment with improvements in a risk-free environment.
Increased emphasis on sustainability
The global manufacturing landscape has shown an increasing emphasis on environmental impact, and this is only set to continue. Many current predictive analytics use cases already benefit this aspect through increased resource efficiency, but more use cases that directly improve sustainability goals are sure to appear.
Wrapping Up
Hopefully, this blog has helped your understanding of how predictive analytics is powering Smart Manufacturing. If you’re curious about how it’s being used in other industries, check out our other blogs on: